Fixtures, JIGS, and test rigs
A makeshift “device simulator” took the functionality of our product and broke it out into the far more luxurious confines of a grapefruit-sized blue box. Unencumbered by power limitations or small, underdeveloped physical mechanisms, we were able to iterate less tangible elements like firmware and software interactions.
Frequently during the iterative process it becomes obvious how important it is not just to develop one’s product, but to build and maintain the fixtures and devices that enable the careful testing and development of one’s main invention. This is especially important for “breaking out” PCB and electronics prototyping from the physical manufacturing and testing of individual device parts.
A perfect example of a fixture development process can be found in a specific metal spring we made especially for our first product—a spring that not only doesn’t exist on the market, and which would have been expensive and time consuming to iterate with an outside agency.
And so we had to get creative.
Etching metal contact wipers on the Bantam Tools CNC Mill.



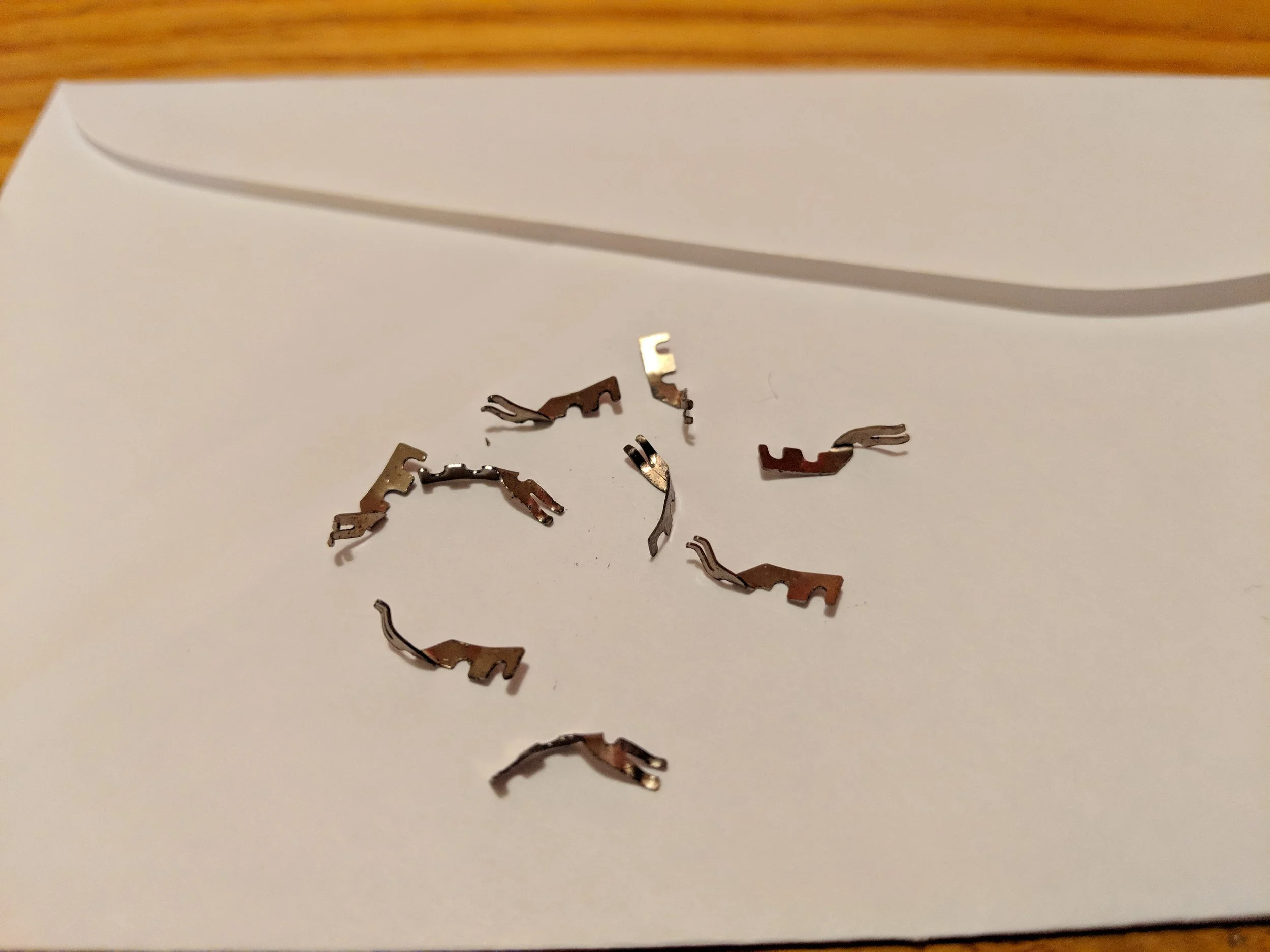




By using a small CNC milling machine, we were able to iterate several versions of contact wipers until we found a design that met all of our requirements.
Once we had settled on a design, we realized we would need quite a lot more springs than we could produce on a CNC mill, and experimented with etching in bulk. See that journey here. Instead, to arrive at the fixturing itself, we’ll fast forward to the next challenge that emerged: bending.
bend it like… well, A fixture.
The problem:
Bending a metal spring the exact same way, every time. On a budget.
For this challenge, we had to do some CAM.
Fusion 360’s CAM package was used to make our first metal-stamping dies, milled from aluminum stock.
Aluminum dies stamping copper contacts was never going to work for long: the small delicate bits of the dies would be worn down quickly by the competing hardness of copper. But before investing time and resources into ordering dedicated steel dies, we were committed to testing the functionality of the form.
Once we verified our metal-forming die worked as promised, we sent our model to Shapeways to be 3D-printed in steel using their own bronze-infusing process. When the parts came back to use, we built our final fixture.
The comparative hardness of steel to copper allows this die to be used hundreds or thousands of times without significant wear, creating an efficient and repeatable method for producing springs with constant bends at a fraction of the cost of outsourcing to spring manufacturers.
more examples!
Other support devices we’ve created range from injection molding fixtures to pogo pin uploaders to device longevity and robustness testers. Read more about those innovations on their respective pages!